LOGISTICA DI MAGAZZINO PER T LOGIST
Manuale
l presente documento è una guida per l’utilizzo del modulo Logist.
Il documento ne descrive le funzionalità dettagliando le interazioni con funzioni e altri moduli della suite Logica.
Sommario
Premessa
Definizioni e Terminologia
2.1 Descrizioni flussi in entrata2.2 Utilizzo della merce (es. scarico carta e reso di produzione)Configurazione del Software
3.1 Configurazione Utenti3.2 Configurazione Locazioni3.3 Configurazioni Causali3.4 Configurazione Anagrafiche MagazzinoDescrizione delle Funzioni Software
4.1 Accesso al modulo SW4.2 Etichettatura materiale
4.3 Entrata materiale4.4 Stoccaggio materiale4.5 Invio a produzione4.6 Rientro da produzione4.7 Inventario4.8 Operazioni Speciali
1.0 Premessa
Logist è il modulo software dedicato alla logistica di magazzino, ovvero alla movimentazione dei materiali, integrato con il modulo per la gestione delle commesse ProtoCOMM ed il modulo per la gestione del magazzino ProtoMAG.
Le funzioni software del sistema di logistica sono utilizzate da terminale bar-code (“pistola”), ma sono disponibili anche da interfaccia web dedicata.
In questo documento sono descritte in particolare le funzionalità disponibili per la gestione dei materiali di tipo “materia prima”, in primis la carta; quindi con il termine materiale si intenderà genericamente una materia prima.
Nel seguito verranno descritte le configurazioni che devono essere realizzate nel sistema e quindi le funzioni del software, con le relative specifiche di funzionamento e si utilizzerà il termine “pacco” per indicare un vero pacco/risma oppure un pallet, ovvero un insieme di fogli da considerare come un tutt’uno ed identificati da una etichetta in bar-code univoca.
2.0 Definizioni e Terminologia
Per poter avviare un progetto di implementazione di un sistema di gestione logistica ci sono una serie di attività preliminari da fare.
Si deve innanzitutto mappare ed organizzare il magazzino (o i magazzini) suddividendoli in singole Locazioni (aree fisiche di stoccaggio dei materiali) che consentiranno di identificare la singola ubicazione della merce giacente in magazzino.
La mappatura fisica delle aree consentirà anche una riorganizzazione delle movimentazioni logistiche in quanto il sistema consentirà di tracciare l’entrata delle merci temporaneamente allocabile in una singola area generica di scarico, ordinare la merce nella locazione desiderata e tracciare gli scarichi e le uscite della stessa.
Dovrà poi essere fatto un inventario con l’etichettatura di tutta la merce e ogni etichetta corrisponderà pertanto ad un singolo pacco/pallets ecc. ed in base all’ubicazione associata creeranno una sorta di mappa virtuale di tutto la merce in magazzino.
Con questo sistema sarà anche possibile avere la tracciabilità dei lotti utilizzati nelle singole commesse.
2.1 Descrizione flussi in entrata
All’arrivo della merce ordinata il magazziniere registrerà un documento di entrata merce partendo dall’ordine ed andando a confermare/modificare tutte le quantità ordinate, registrando i pacchi/pallets in ingresso.
Questo consentirà di etichettare la merce appena entrata, riscontrare l’ordine e depositare la merce stessa nell’ubicazione prestabilita. L’associazione merce in ingresso con il ddt di carico e con l’etichetta ne consente la tracciabilità del lotto.
2.2 Utilizzo della merce (es. scarico carta e reso produzione)
Al momento della consegna in macchina della carta il magazziniere, sulla base dell’impegno su commessa, scaricherà la carta portata a bordo macchina cliccando sulle rispettive etichette. Questa operazione scarica la carta (di uno specifico lotto) su commessa.
Se dalla produzione dovesse avanzare della merce rispetto a quella scaricata sarà sufficiente fare un reso andando ad associare una nuova quantità (quella residua) al quel lotto/etichetta.
3.0 Configurazione del Software
Per l’utilizzo di Logist, oltre alle configurazioni di sistema che vengono attivate in fase di installazione del software, occorre analizzare e realizzare le configurazioni descritte nei seguenti paragrafi.
Controllare anche RDAServer: http://192.168.0.6:8081/books/proto-project/page/rdaserver20-come-servizio
Per l’utilizzo di Logist, oltre alle configurazioni di sistema che vengono attivate in fase di installazione del software, occorre analizzare e realizzare le configurazioni descritte nei seguenti paragrafi.
Controllare anche RDAServer: http://192.168.0.6:8081/books/proto-project/page/rdaserver20-come-servizio
3.1 Configurazione Utenti
Come per qualunque altro modulo software occorre configurare gli utenti che sono abilitati all’utilizzo di Logist.
Questo viene eseguito all’interno del modulo Sys, configurando innanzitutto i Profili:
e quindi gli Utenti ad essi associati:
3.2 Configurazione Locazioni
All’interno degli Archivi del modulo ProtoMAG vanno configurate le Locazioni nelle quali si intende movimentare i materiali; ogni locazione è associata ad un deposito.
Logist prevede la configurazione di alcune Locazioni di default, per le seguenti operazioni:
etichettatura materiale
entrata materiale
rientro materiale
Per l’etichettatura materiale, se la locazione non viene specificata, la locazione di default è la seguente:
Logist assegna al materiale in entrata la seguente locazione di default:
Analogamente Logist assegna al materiale che rientra dalla produzione la seguente locazione di default:
Le tre Locazioni di sopra vanno quindi sempre configurate in Logist.
3.3 Configurazione Causali
All’interno degli Archivi del modulo Mag vanno configurate le nuove Causali utilizzate in Logist ed aggiornate quelle esistenti per essere utilizzate in Logist.
3.4 Configurazione Anagrafiche di magazzino
All’interno delle Anagrafiche di magazzino va attivato il check-box “Visibile da altro sistema” per ogni articolo che si vuole gestire in Logist:
4.0 Descrizione delle funzioni software
Per l’utilizzo di Logist, oltre alle configurazioni di sistema che vengono attivate in fase di installazione del software, occorre analizzare e realizzare le configurazioni descritte nei seguenti paragrafi.
Per l’utilizzo di Logist, oltre alle configurazioni di sistema che vengono attivate in fase di installazione del software, occorre analizzare e realizzare le configurazioni descritte nei seguenti paragrafi.
4.1 Accesso al modulo SW
Dopo aver selezionato il proprio login occorre indicare la password e premere il pulsante OK, per accedere al sistema, oppure il pulsante CANCELLA per annullare.
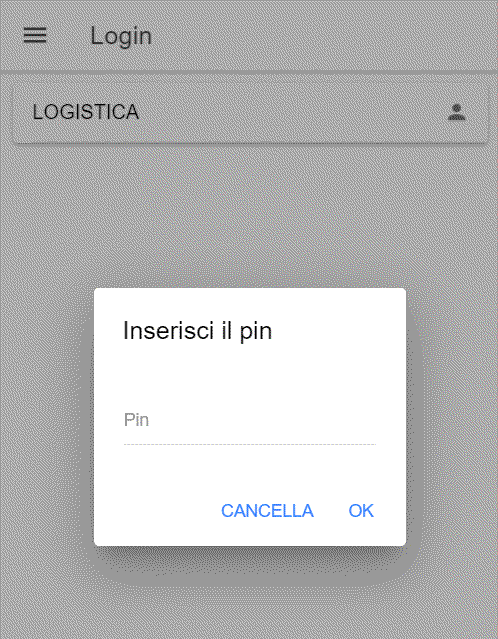
Una volta premuto il pulsante OK, appare il menù delle funzioni disponibili:
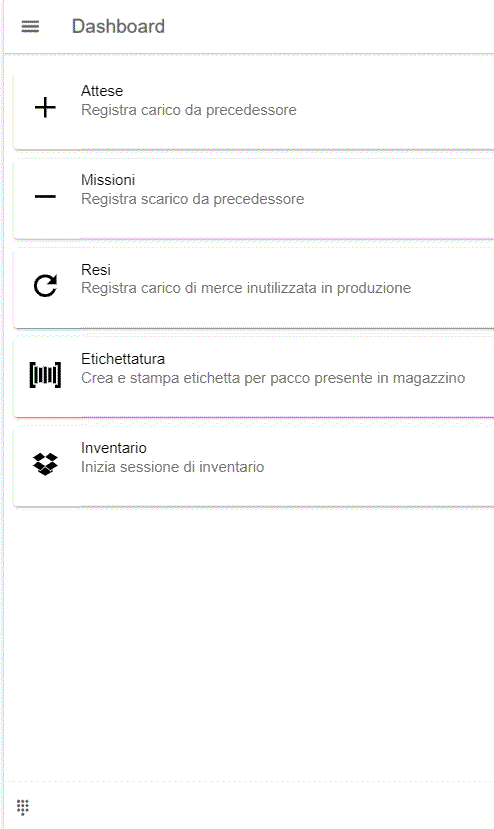
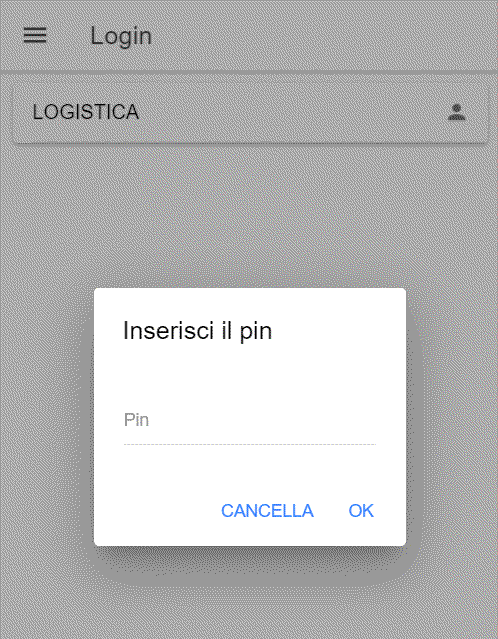
Una volta premuto il pulsante OK, appare il menù delle funzioni disponibili:
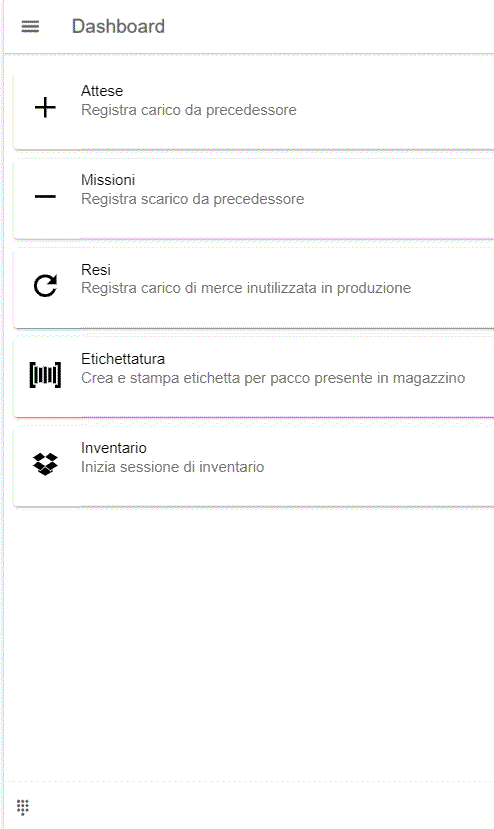
4.2 Etichettatura materiale
Come detto in precedenza, la prima operazione da eseguire è l’etichettatura del materiale, che può avvenire in uno dei seguenti modi:
mediante la relativa voce di menu, se il materiale è già a magazzino
durante l'entrata a magazzino del materiale
durante l'esecuzione dell'inventario se viene rilevato un materiale privo di etichetta
Qui di seguito descriviamo l’operazione di etichettatura.
Selezionando la voce di menù “Etichettatura”, verrà mostrata la lista degli articoli di magazzino da etichettare:
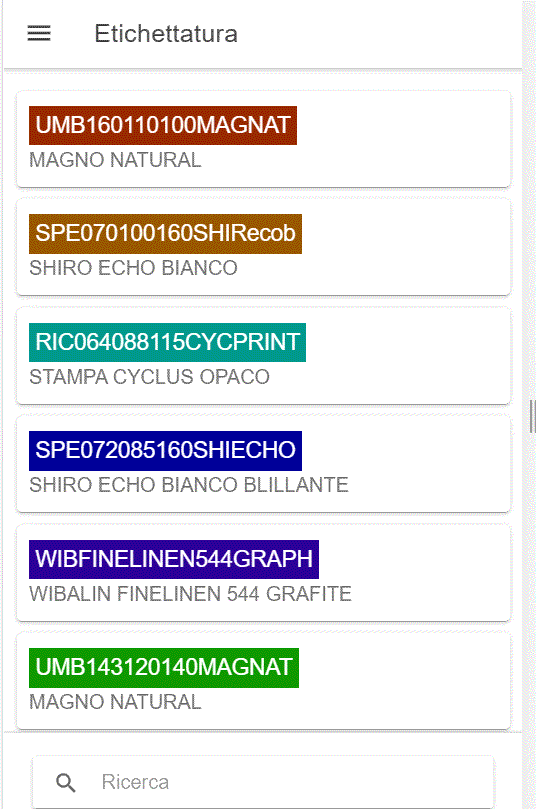
mediante la relativa voce di menu, se il materiale è già a magazzino
durante l'entrata a magazzino del materiale
durante l'esecuzione dell'inventario se viene rilevato un materiale privo di etichetta
Qui di seguito descriviamo l’operazione di etichettatura.
Selezionando la voce di menù “Etichettatura”, verrà mostrata la lista degli articoli di magazzino da etichettare:
Mediante il mouse è possibile scorrere la lista, all’interno della quale si può eseguire una ricerca indicando codice oppure nome, anche solo parzialmente, di un articolo di magazzino:
Una volta selezionato l’articolo per il quale generare l’etichetta o le etichette (è infatti possibile stampare più etichette in presenza di più pacchi), per ogni etichetta in bar-code che si intende generare, è sufficiente indicare i numeri di fogli (nel campo “FG”) che sono sul pacco e quindi premere il pulsante “Registra e stampa”.
Automaticamente a Mag verrà generato un documento con causale “ETIC_LIB”, corrispondente all’etichetta bar-code e con locazione “ET1”; nel menù Archivi/Pacchi del pannello principale di Mag si troveranno le informazioni del nuovo pacco:
Qualora invece venga scansionata una locazione, corrispondente alla posizione in cui si trova il materiale a magazzino, a Mag verrà generato un documento ancora con causale “ETIC_LIB” ma con la locazione scansionata.
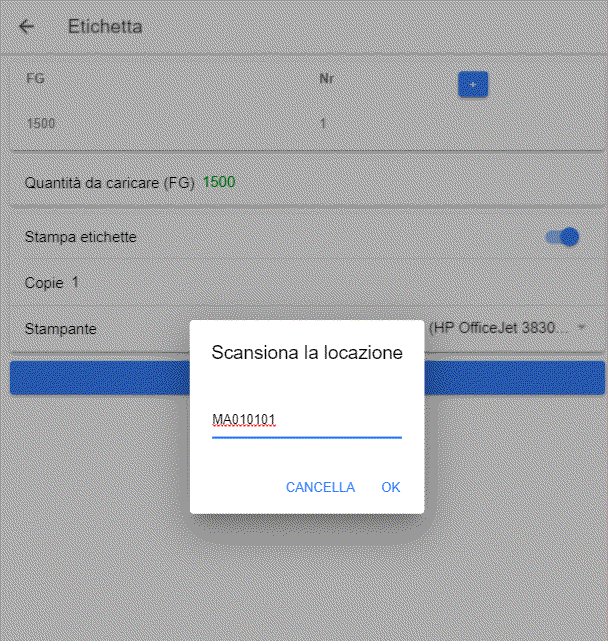
Qualora la giacenza a Mag sia inferiore a quella rilevata mediante l’etichettatura, a Mag verrà generato anche un documento con causale “RETP_L”, per rettificare la quantità risultante a sistema.
Nel menù “Utilità” del pannello principale di Mag è disponibile la voce “Quadrature logistica”, selezionando la quale è possibile visualizzare l’elenco dei materiali la cui giacenza a Mag e a Logist differisce, in modo che possa essere rettificata:

Nel menù “Utilità” del pannello principale di Mag è disponibile la voce “Quadrature logistica”, selezionando la quale è possibile visualizzare l’elenco dei materiali la cui giacenza a Mag e a Logist differisce, in modo che possa essere rettificata:

4.3 Entrata materiale
Al materiale, oltre che mediante la funzione di “Etichettatura”, può essere assegnata un’etichetta con codice a barre direttamente al suo ingresso a magazzino.
All’interno del menù “Attese” sono disponibili le funzioni per registrare un documento di “entrata materiale” e stampare contemporaneamente le etichette per esso.
Il materiale può essere di proprietà dell’azienda oppure di un proprio cliente.
Nel menù “Attese” viene quindi visualizzata la lista dei documenti di tipo “Ordine a fornitore” (causale “ORD”) e “Attesa merce cliente” (causale “BEM_L”) registrati in Mag e riferiti rispettivamente ad un fornitore e ad un cliente:
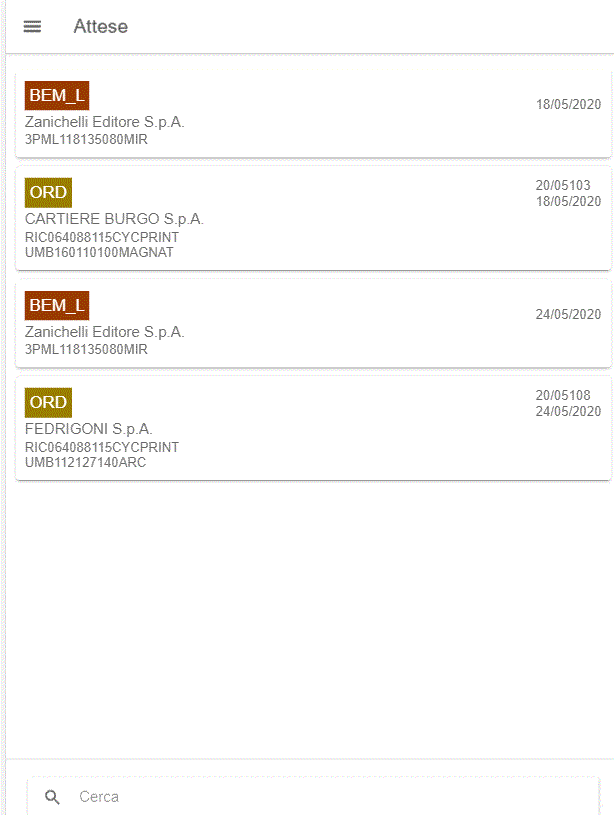
E’ quindi possibile eseguire una ricerca per fornitore (nel caso di “ORD”) e cliente (nel caso di “BEM_L”) e per numero documento, ad esempio:
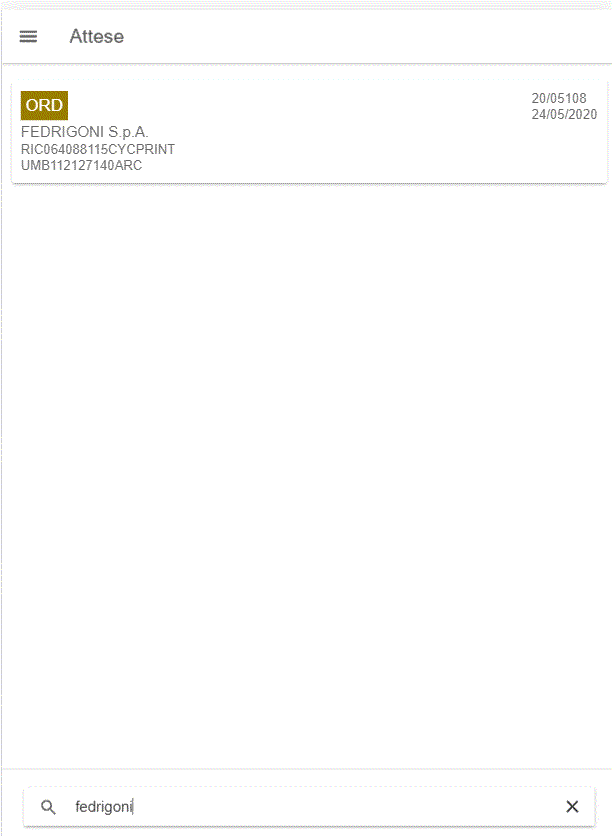
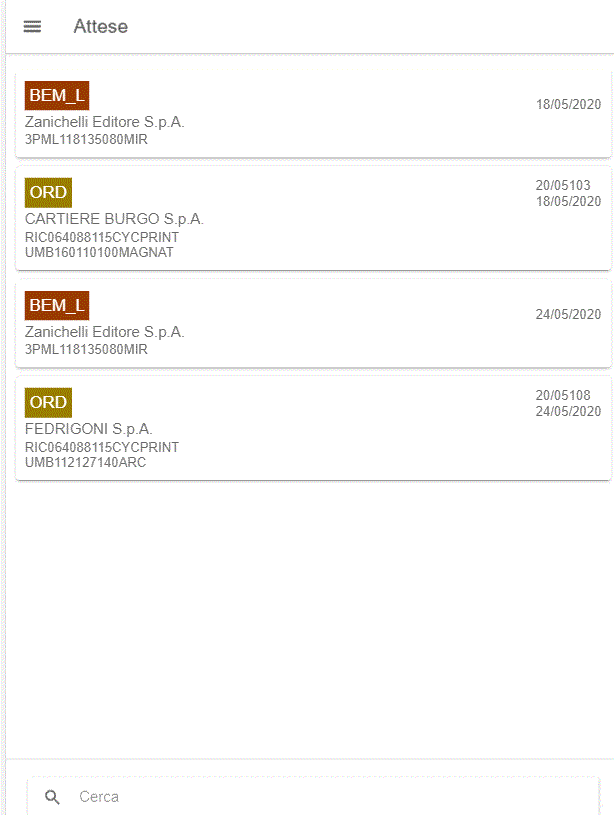
E’ quindi possibile eseguire una ricerca per fornitore (nel caso di “ORD”) e cliente (nel caso di “BEM_L”) e per numero documento, ad esempio:
dopodichè registrare i dati identificativi (numero e data, eventualmente cambiandola e confermandola con il pulsante DONE) del documento di trasporto ricevuto dal fornitore e successivamente le quantità ricevute per ognuno dei materiali:
modificando eventualmente il peso teorico del materiale, indicandolo nel campo “Peso reale”:
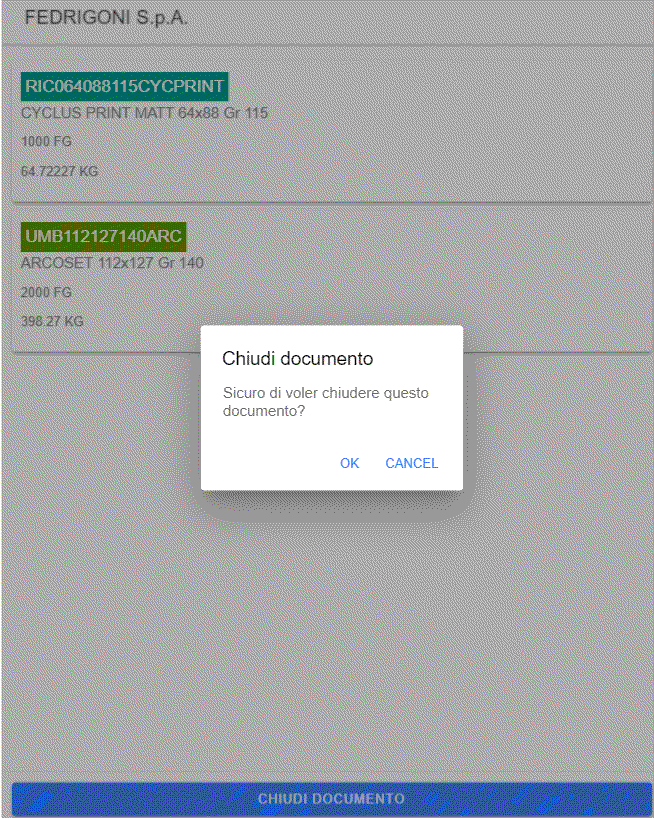
A Mag verrà automaticamente registrato un documento con causale “CAR_L” (in caso di fornitore) oppure con causale “CAR_C_L” (in caso di cliente):
Il materiale viene automaticamente caricato nella locazione IN1; lo si può poi collocare in altra locazione mediante l’operazione di stoccaggio:
Qualora la merce ricevuta sia in quantità inferiore a quella ordinata e non se ne debba ricevere altra, da Mag occorre aprire il documento di “carico” e saldare le righe relative.
Qualora un DdT riepiloghi più ordini, è possibile registrare il DdT in più momenti; per questo è fondamentale impostare sempre gli stessi dati per numero e data del DdT stesso.
4.4 Stoccaggio materiale
Mediante l’operazione di stoccaggio è possibile in qualunque momento spostare il materiale da una locazione ad un’altra.
Nel menù principale premere il pulsante in basso a sinistra:
Quindi scansionare il bar-code del pacco che si intende spostare:
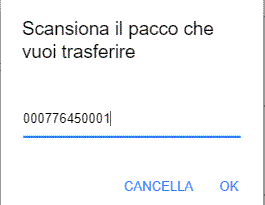
ed infine scansionare il bar-code della nuova locazione in cui posizionare il materiale:
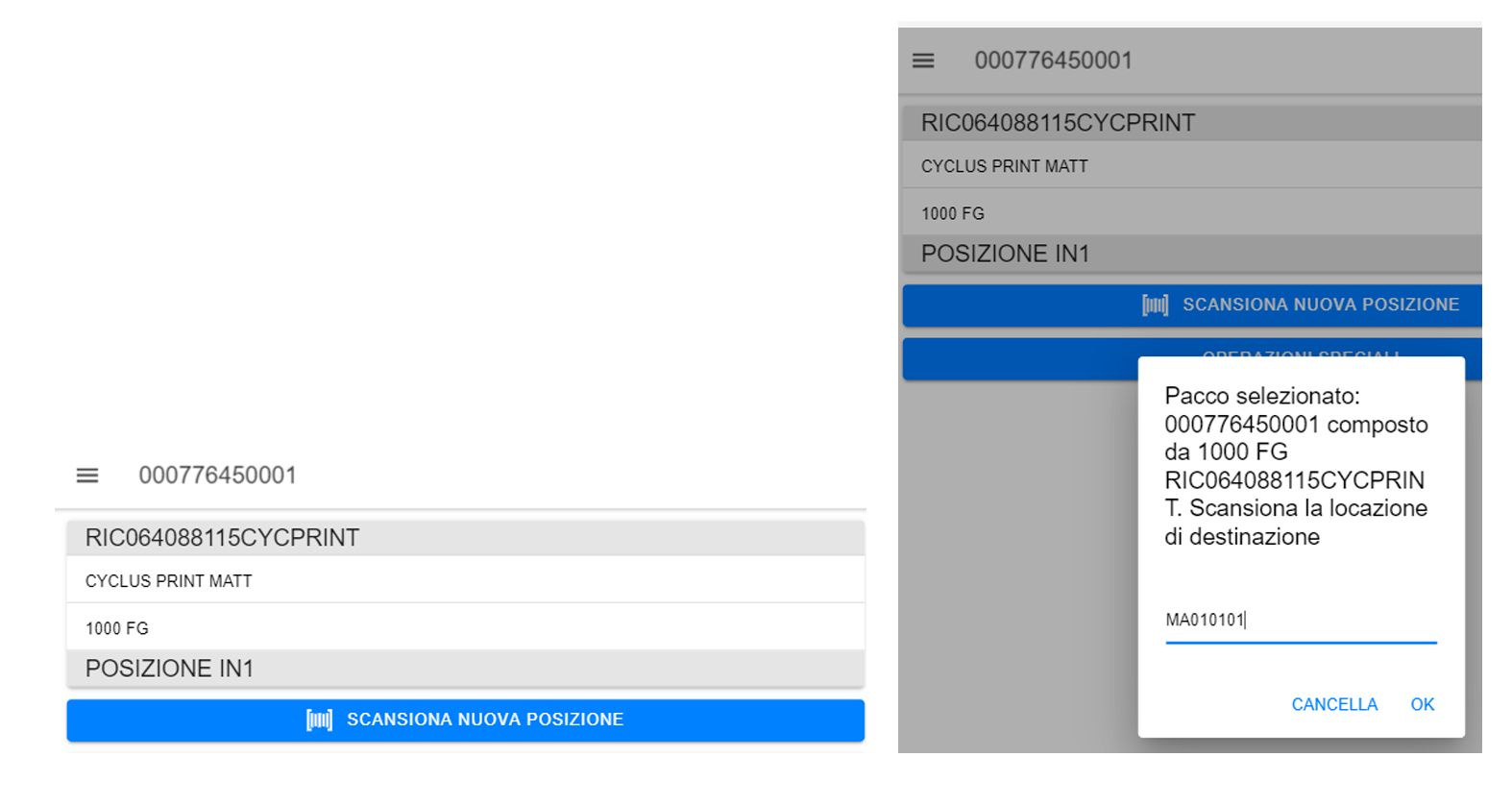
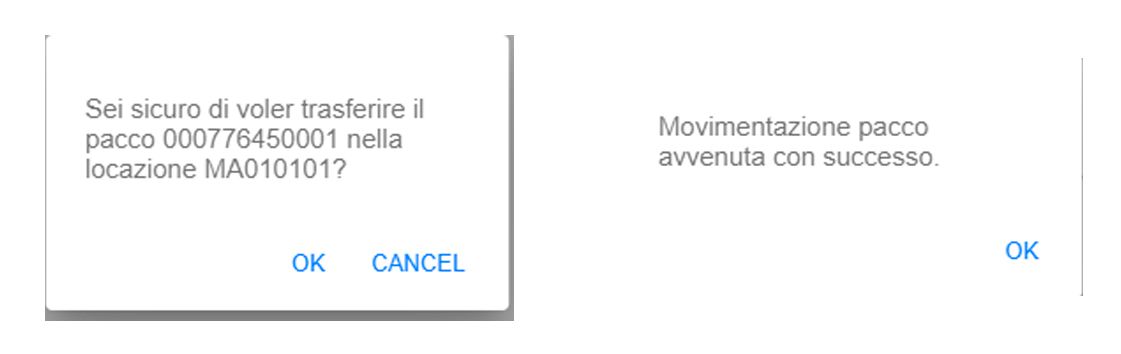
A Mag viene automaticamente registrato un documento con causale “TRSLOC” (cambio locazione) e nel menù Archivi\Pacchi la carta verrà visualizzata nella nuova locazione:

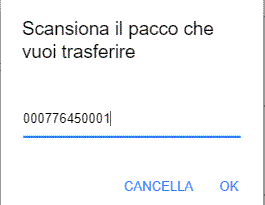
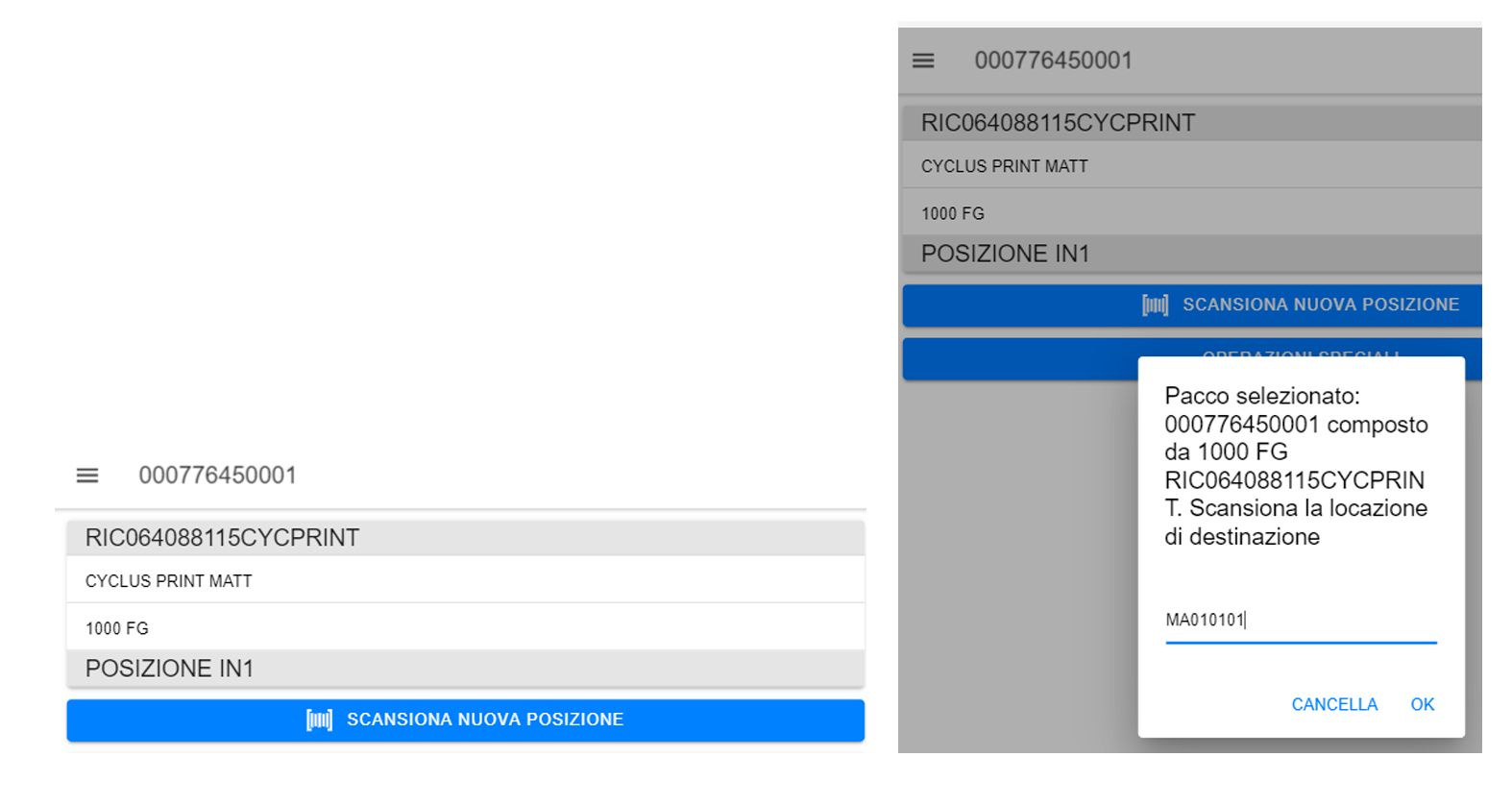
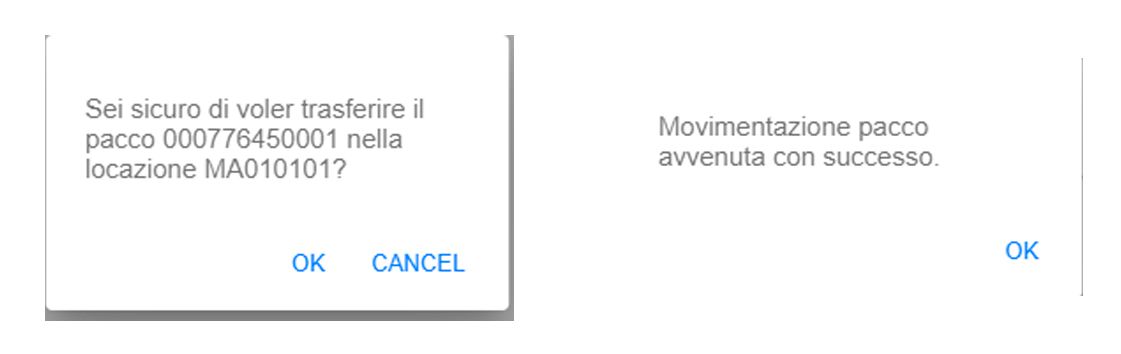

4.5 Invio a produzione
L’invio a produzione, ovvero lo scarico, di un materiale è gestito nel menù Missioni, nel quale sono quindi selezionabili le commesse per le quali sono stati eseguiti degli “Impegni automatici” in Comm.
Per prima cosa occorre ricercare la commessa per la quale eseguire l’operazione mediante scrittura esplicita del numero della commessa (intesa come registro e numero) oppure mediante scansione dell’etichetta in bar-code del cliente oppure della commessa (inseriti nel report di commessa) ed il sistema proporrà la lista degli “impegni automatici” registrati per essa:
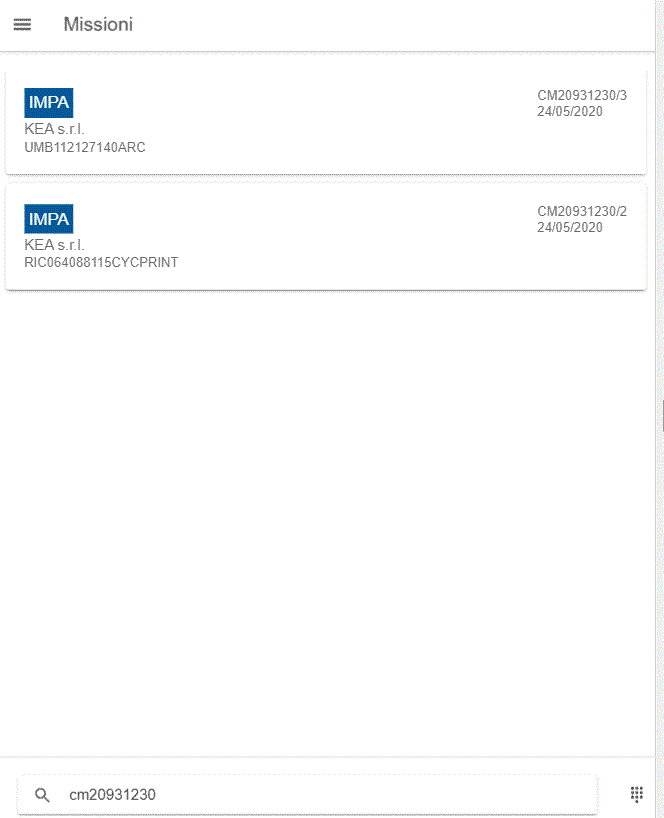
Si selezionerà quindi l’impegno relativo alla carta da portare in produzione e si scansioneranno i pacchi che il sistema proporrà per la carta corrispondente, fino al raggiungimento della quantità di carta richiesta; a questo punto, si potrà scegliere fra portare in produzione l’intero pacco oppure solo la quantità di materiale effettivamente richiesto, deselezionando “Movimenta intero collo/pallet/pacco/udc”:
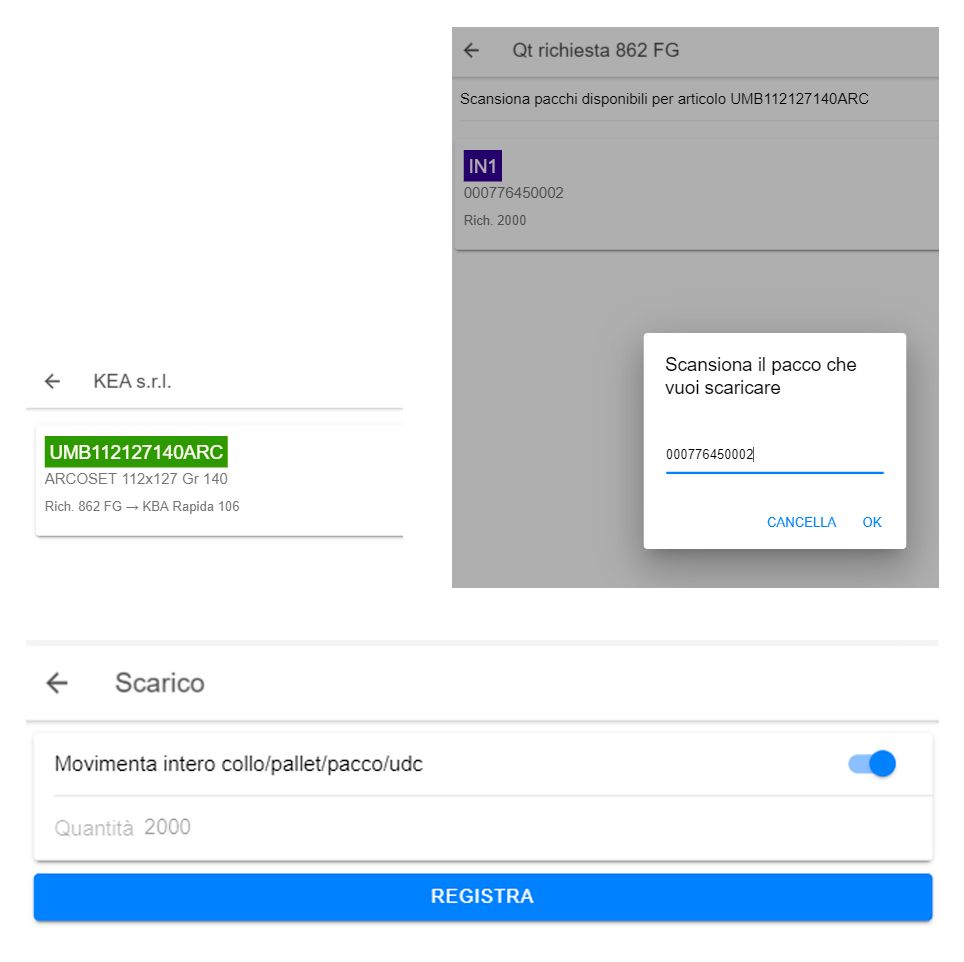
Premere quindi Registra.
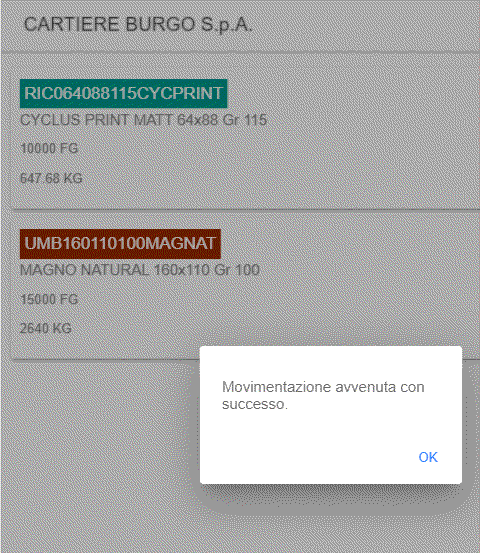
Premere quindi OK e successivamente “Chiudi documento” per far ritorno al menù principale.
A Mag verrà automaticamente registrato un documento con causale “P_RECM_L”, di scarico a produzione.
Nel menù Missioni vengono anche gestite le uscite di materiale, ad esempio per conto lavoro:
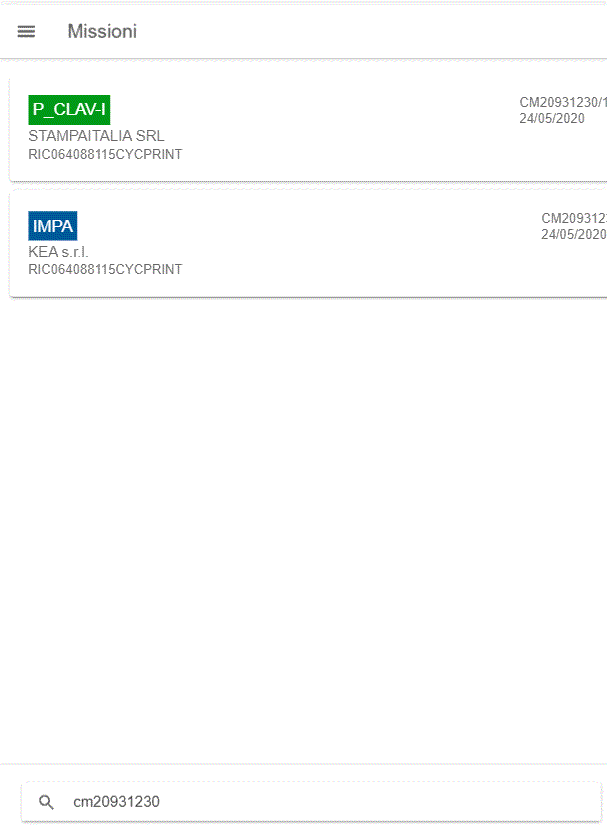
In tale caso, a fronte di un ordine ad un fornitore di conto lavoro al quale venga fornita della carta, a Mag viene registrato un documento con causale “P_CLAV_I”, prelevando come predecessore, oltre all’ordine a fornitore, anche la carta impegnata in commessa.
A fronte della esecuzione in Logist delle medesime operazioni eseguite per lo “Invio a produzione”, la causale del documento a Mag viene automaticamente rettificata in “R_CLAV_I”, ad attestare un possibile rientro di carta dall’esterno (analogamente a quanto visto per l’attesa reso dalla produzione interna).
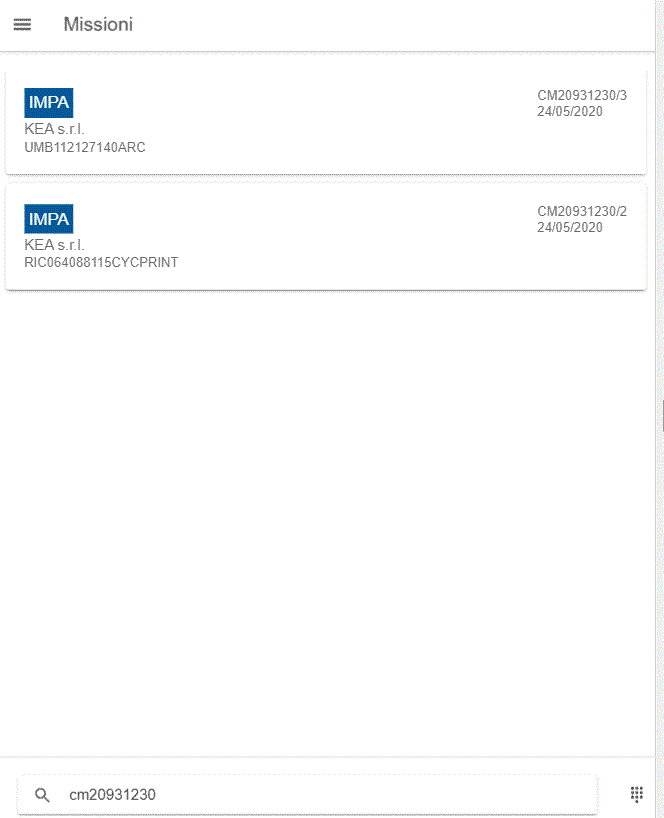
Si selezionerà quindi l’impegno relativo alla carta da portare in produzione e si scansioneranno i pacchi che il sistema proporrà per la carta corrispondente, fino al raggiungimento della quantità di carta richiesta; a questo punto, si potrà scegliere fra portare in produzione l’intero pacco oppure solo la quantità di materiale effettivamente richiesto, deselezionando “Movimenta intero collo/pallet/pacco/udc”:
Premere quindi Registra.
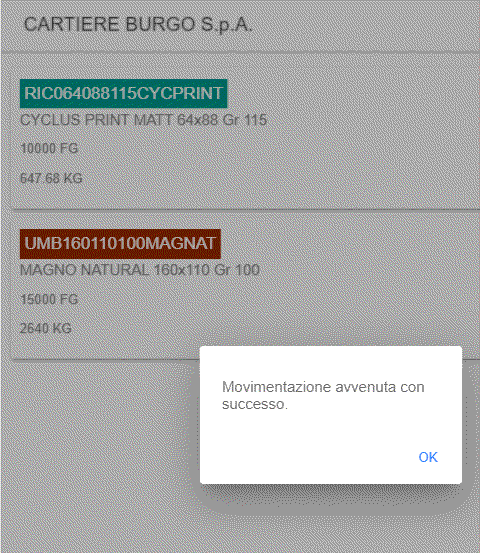
Premere quindi OK e successivamente “Chiudi documento” per far ritorno al menù principale.
A Mag verrà automaticamente registrato un documento con causale “P_RECM_L”, di scarico a produzione.
Nel menù Missioni vengono anche gestite le uscite di materiale, ad esempio per conto lavoro:
In tale caso, a fronte di un ordine ad un fornitore di conto lavoro al quale venga fornita della carta, a Mag viene registrato un documento con causale “P_CLAV_I”, prelevando come predecessore, oltre all’ordine a fornitore, anche la carta impegnata in commessa.
A fronte della esecuzione in Logist delle medesime operazioni eseguite per lo “Invio a produzione”, la causale del documento a Mag viene automaticamente rettificata in “R_CLAV_I”, ad attestare un possibile rientro di carta dall’esterno (analogamente a quanto visto per l’attesa reso dalla produzione interna).
4.6 Rientro da produzione
I rientri del materiale dalla produzione vengono gestiti nel menù “Resi”, nel quale vengono presentati tutti i documenti di “Invio a produzione” precedentemente emessi ed in attesa di rientro del materiale dalla produzione:
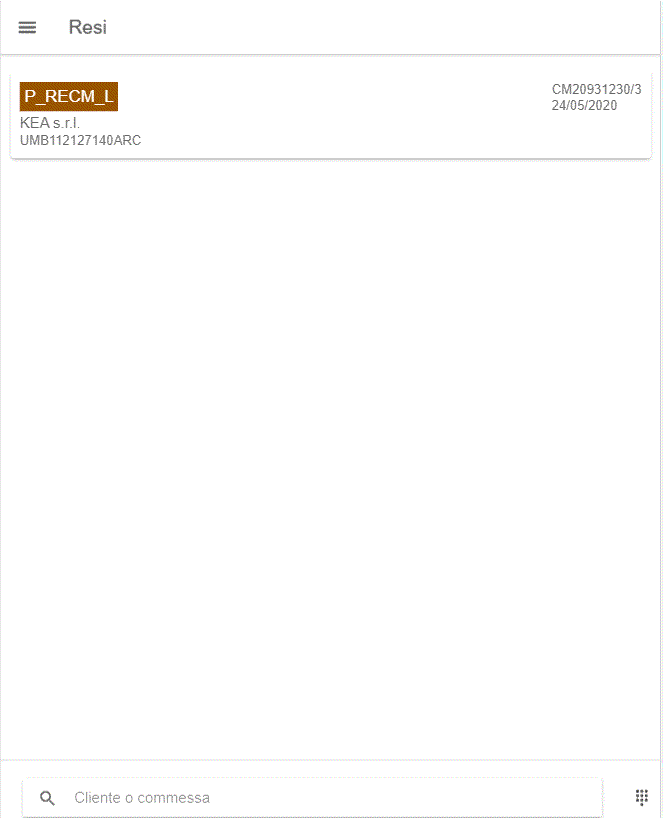
Si possono eseguire le stesse operazioni di ricerca disponibili per lo “Invio a produzione”.
Una volta indicati i fogli rientrati dalla produzione, si premerà “Registra e stampa”; verrà quindi stampata una nuova etichetta in bar-code da apporre sul pacco rientrato, che automaticamente verrà posizionato nella locazione “RESI1”, dalla quale potrà poi essere spostato nella locazione desiderata.
A Mag verrà automaticamente registrato un documento con causale “RECOM_L”, di reso
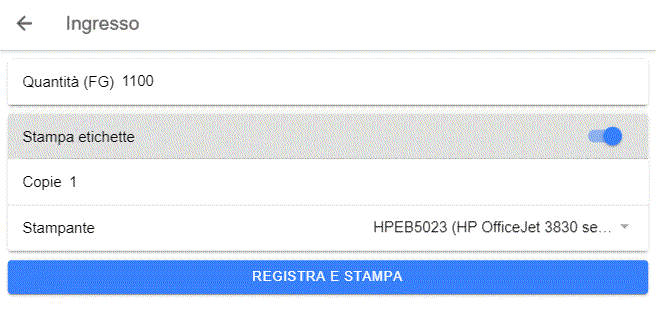
I rientri del materiale dalla produzione vengono gestiti nel menù “Resi”, nel quale vengono presentati tutti i documenti di “Invio a produzione” precedentemente emessi ed in attesa di rientro del materiale dalla produzione:
Si possono eseguire le stesse operazioni di ricerca disponibili per lo “Invio a produzione”.
Una volta indicati i fogli rientrati dalla produzione, si premerà “Registra e stampa”; verrà quindi stampata una nuova etichetta in bar-code da apporre sul pacco rientrato, che automaticamente verrà posizionato nella locazione “RESI1”, dalla quale potrà poi essere spostato nella locazione desiderata.
A Mag verrà automaticamente registrato un documento con causale “RECOM_L”, di reso
4.7 Inventario
PRIMA DI TUTTO fare una copia dell'ambiente di MAG su SIMULA
La copia va fatta prima di entrare in sessione inventariale.
L’esecuzione dell’inventario completo di magazzino viene attivata dal menù Utilità di Mag, selezionando la voce “Apertura sessione inventariale”:
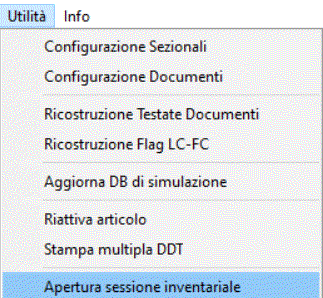
Qualora si tenti di eseguire l’inventario prima di eseguire quanto sopra, a terminale verrà mostrato il seguente messaggio:

Dopo avere attivato l’esecuzione dell’inventario, si può procedere.
Per ogni locazione scansionata:
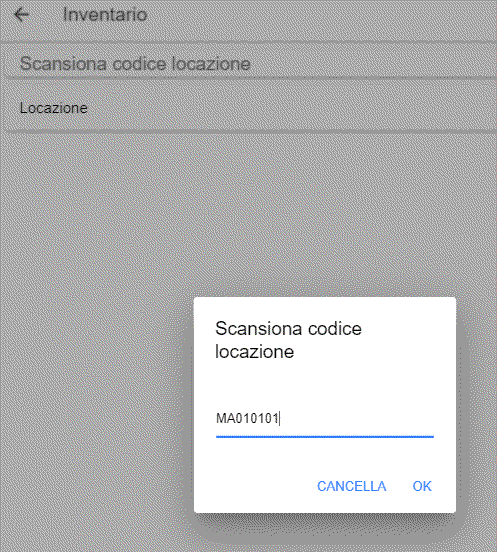
occorre scansionare i materiali ivi presenti:
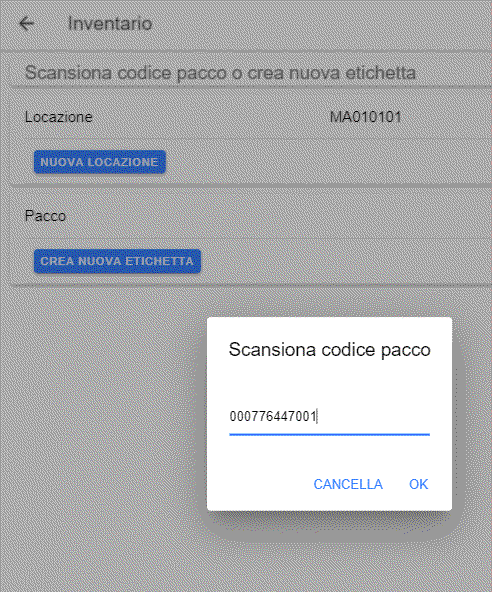
indicando, per ognuno, la quantità effettivamente rilevata a magazzino:
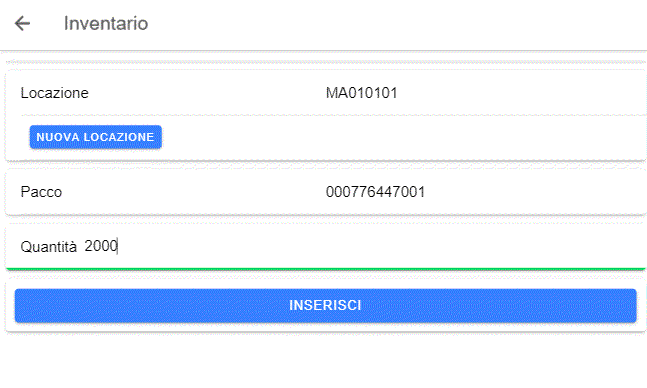
e poi premendo il pulsante Inserisci:
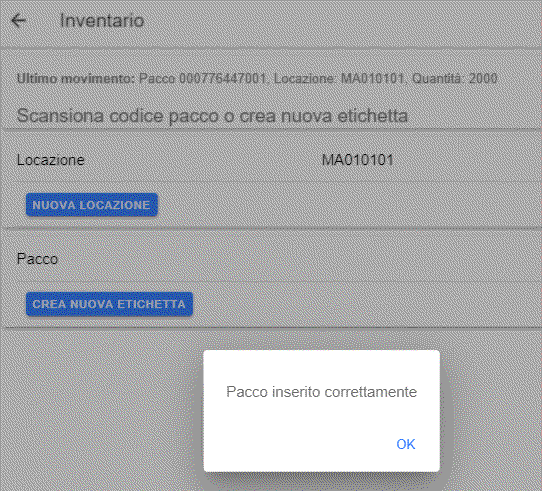
Come detto in precedenza è possibile etichettare dei materiali in fase di esecuzione dell’inventario selezionando “Crea nuova etichetta”.
Nel caso vengano create nuove etichette è necessario che vengano a loro volta scansionate per aggiungerle a quelle rilevate durante la sessione inventariale.
Terminati di scansionare i materiali di una locazione si passa quindi ad una nuova locazione selezionando “Nuova locazione”.
Una volta terminata l’esecuzione dell’inventario da terminale, a Mag si seleziona la voce “Chiusura sessione inventariale” del menù Utilità.
A Mag verranno quindi registrati automaticamente i documenti con causali “RETP_L” e “RETN_L”, rispettivamente di rettifica positiva e negativa, allineando le giacenze del sistema centrale a quello della logistica, sulla base delle effettive giacenze rilevate su quest’ultimo.
PRIMA DI TUTTO fare una copia dell'ambiente di MAG su SIMULA
La copia va fatta prima di entrare in sessione inventariale.
L’esecuzione dell’inventario completo di magazzino viene attivata dal menù Utilità di Mag, selezionando la voce “Apertura sessione inventariale”:
Qualora si tenti di eseguire l’inventario prima di eseguire quanto sopra, a terminale verrà mostrato il seguente messaggio:
Dopo avere attivato l’esecuzione dell’inventario, si può procedere.
Per ogni locazione scansionata:
occorre scansionare i materiali ivi presenti:
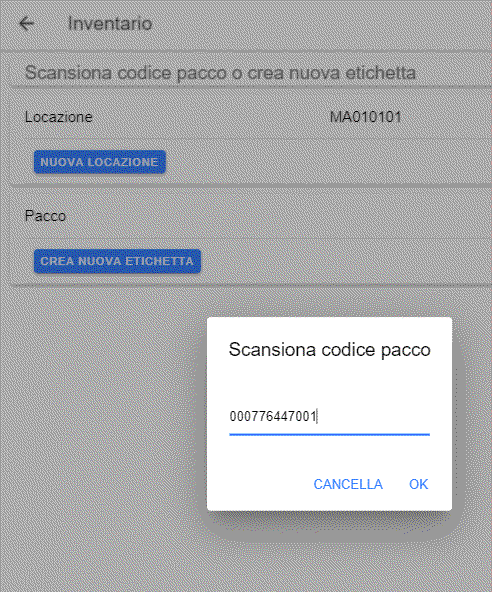
indicando, per ognuno, la quantità effettivamente rilevata a magazzino:
e poi premendo il pulsante Inserisci:
Come detto in precedenza è possibile etichettare dei materiali in fase di esecuzione dell’inventario selezionando “Crea nuova etichetta”.
Nel caso vengano create nuove etichette è necessario che vengano a loro volta scansionate per aggiungerle a quelle rilevate durante la sessione inventariale.
Terminati di scansionare i materiali di una locazione si passa quindi ad una nuova locazione selezionando “Nuova locazione”.
Una volta terminata l’esecuzione dell’inventario da terminale, a Mag si seleziona la voce “Chiusura sessione inventariale” del menù Utilità.
A Mag verranno quindi registrati automaticamente i documenti con causali “RETP_L” e “RETN_L”, rispettivamente di rettifica positiva e negativa, allineando le giacenze del sistema centrale a quello della logistica, sulla base delle effettive giacenze rilevate su quest’ultimo.
4.8 Operazioni Speciali
Oltre alle operazioni sopra descritte, è possibile eseguire delle “operazioni speciali”, quali la ristampa di una etichetta in bar-code oppure degli scarichi di materiale non legati a commessa, ovvero “generici”, eventualmente distinti per tipologia (ad es. si possono differenziare gli scarichi di materiale quando lo si utilizza per delle “campionature”).
Tali operazioni sono attivabili configurando in maniera opportuna determinate causali di magazzino; qui di seguito se ne illustra una ad esempio.
Per accedere a queste operazioni occorre scansionare un pacco e quindi selezionare la voce “Operazioni speciali”.
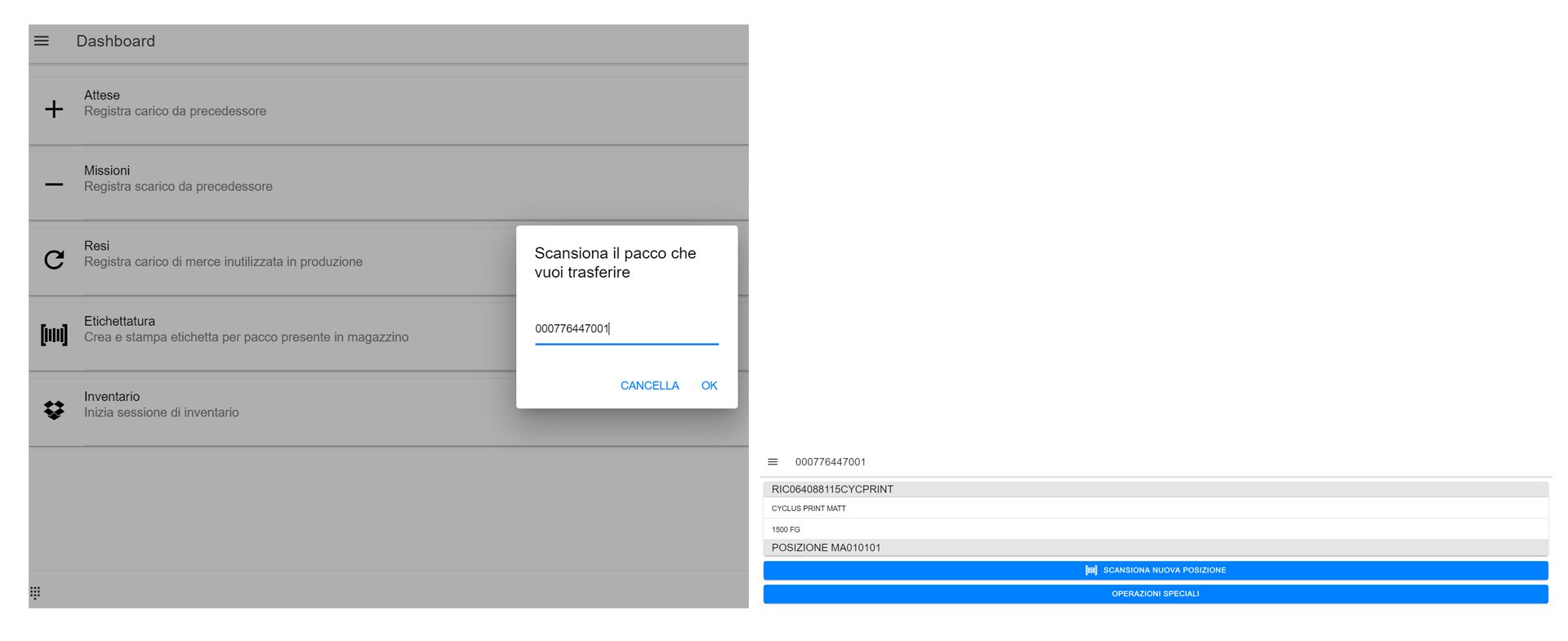
Per ristampare un’etichetta in bar-code ovviamente va selezionata la voce di menù corrispondente:

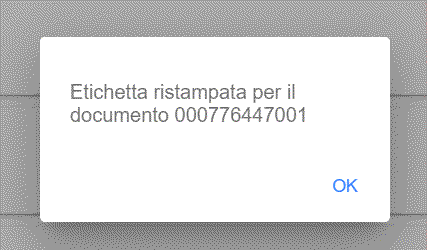
Per eseguire invece, ad esempio, uno “scarico generico” va analogamente selezionata la voce di menù corrispondente ed indicata l’effettiva quantità di materiale da scaricare (lasciare attivato “Movimenta intero collo/pallet/pacco/udc” in caso la quantità da scaricare sia la totale):


A Mag verrà automaticamente registrato il corrispondente movimento di “scarico generico”.
Oltre alle operazioni sopra descritte, è possibile eseguire delle “operazioni speciali”, quali la ristampa di una etichetta in bar-code oppure degli scarichi di materiale non legati a commessa, ovvero “generici”, eventualmente distinti per tipologia (ad es. si possono differenziare gli scarichi di materiale quando lo si utilizza per delle “campionature”).
Tali operazioni sono attivabili configurando in maniera opportuna determinate causali di magazzino; qui di seguito se ne illustra una ad esempio.
Per accedere a queste operazioni occorre scansionare un pacco e quindi selezionare la voce “Operazioni speciali”.
Per ristampare un’etichetta in bar-code ovviamente va selezionata la voce di menù corrispondente:
Per eseguire invece, ad esempio, uno “scarico generico” va analogamente selezionata la voce di menù corrispondente ed indicata l’effettiva quantità di materiale da scaricare (lasciare attivato “Movimenta intero collo/pallet/pacco/udc” in caso la quantità da scaricare sia la totale):
A Mag verrà automaticamente registrato il corrispondente movimento di “scarico generico”.